The disadvantage of the materials transfer using light is, the entire process depends on the optical properties of the transferred material. To reduce the dependence on the optical absorption properties, dynamic release layers (DRL) are introduced. These DRL materials are sensitive to the wavelength used for the LIFT process (often UV) and have the benefit that biologically sensitive materials can be transfered with a low thermal impact due to a reduction in the ablation fluence. The following image shows schematically how the LIFT process works with the introduction of a DRL.
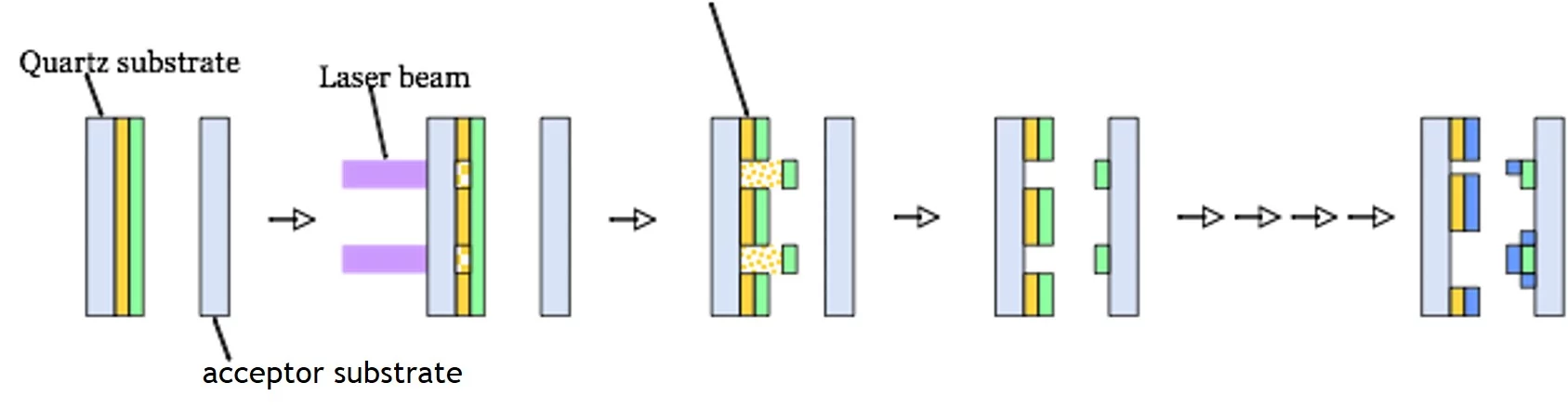
Analysis of the LIFT-Process
Time-Resolved Imaging
Next are four examples of solid and liquid material being transfered. Shadowgraphy is used here to understand the transfer conditions which allow or prevent the transfer a functional pixel onto a receiver substrate.
Applications
Sensor Materials by LIFT
SnO2 Sensors
SnO2 based gas sensors are commercially available and are used to detect volatile organic compounds. Deposition of SnO2 onto these sensors is commonly done by ink-jet printing and a heat treatment to remove solvent residuals. LIFT as a solvent free technique is an ideal candidate to deposit SnO2 onto sensors.Polymer Sensors
(with the the Photonic Processing of Advanced Materials Group at the National Institute for Laser, Plasma and Radiation Physics in Bucharest and the CNR – Istituto di Acustica “O.M. Corbino”, (IDAC – CNR), Rome)
The present project aims at the development of novel fabrication methods for the deposition of patterned single or multilayer thin-film architectures based on mild, “solvent-free” or “dry” material transfer techniques, such as the Laser Induced Forward Transfer. The technique can also be used to deposited multi-layers of polymers or other materials which can not be done using solvent based-methods. These pixels will be the active layers in new developed SAW (surface acoustic wave) and BAW-TFBAR (bulk acoustic wave-thin film bulk acoustic wave resonator) electro-acoustic devices. These sensors can be used as chemical sensor for organic compounds based on chemical selective polymeric materials, as biosensor based on proteins or as gas sensor based on semiconducting oxides and/or catalysts.
OLED Materials by LIFT
(with the Laboratory for Functional Polymers, Empa)Biological Materials by LIFT
(with groups from RPI, Empa, the Georgia Institute of Technology, the Hungarian Academy of Sciences and University of Szeged and the National Institute for Laser, Plasma and Radiation Physics in Bucharest)Tissue engineering integrates biology and materials engineering in developing next-generation medical technologies. Controlling cell adhesion/location, proliferation and patterning is critical in developing next-generation sensing devices and advanced tissue engineered constructs. In depositing sensitive materials such as biomolecules and live cells, the absorption coefficient of the solvent might not be entirely preclude absorption by the biomolecules. Therefore strongly absorbing dynamic release layers are one possible option to protect the biomolecules from UV light.
Other applications
Nanocrystal quantum dots(with the groups from Empa and Penn State University)
Recently, colloidal semiconductor nanocrystal quantum dots (NQDs) has drawn immense attention in the photonics research community due to their superior optical properties and easy processibility. Semiconductor NQDs are nanocrystals that are smaller in size than the diameter of a Bohr exciton in a bulk crystal of the same material. By reducing the size of the nanocrystal core, the quantum confinement of the electronic states in the NQD is increased, with a consequent increase in the exciton energy. In CdSe nanocrystals, for instance, quantum confinement increases the exciton energy from a bulk bandgap of 1.7 eV to any value up to 2.75 eV, and by controlling the particle size during the synthesis, the peak emission wavelength of CdSe(ZnS) core/shell NQDs can be tuned continuously from 470 nm to 650 nm.
Metals and amorphous ceramics
(with the groups from Empa and the University of Southampton)
LIFT with a DRL is also not only useful for sensitive materials, but "hard" materials, such as metals and ceramics can be trasnferred also with high lateral resolution. The application of the DRL and fs laser pulses reveals certain advantages over classical LIFT, where the transfer layer is directly irradiated.
(with the groups from Empa and the University of Southampton)
LIFT with a DRL is also not only useful for sensitive materials, but "hard" materials, such as metals and ceramics can be trasnferred also with high lateral resolution. The application of the DRL and fs laser pulses reveals certain advantages over classical LIFT, where the transfer layer is directly irradiated.